La seguridad en la industria del hidrógeno verde
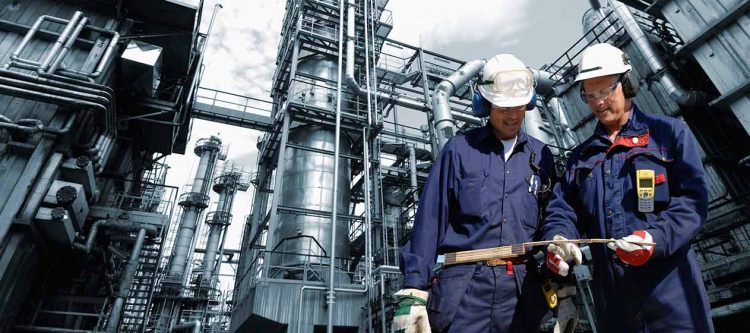
El Green Deal de la UE establece como objetivo la reducción en las emisiones de gases de efecto invernadero (GEI) al 50% en 2030, lo que hace necesario un rápido proceso de descarbonización de la economía. Para ello, entre otras líneas de actuación, la Comisión Europea publicó en julio de este año la Estrategia Europea del Hidrógeno (COM (2020) 301 final), en la que la producción de hidrógeno verde por electrolisis del agua mediante electricidad renovable constituye la tecnología clave.
La estrategia de la Comisión persigue que el hidrógeno pase a ser una parte intrínseca de un sistema energético integrado que disponga en 2030 de, al menos, 40 GW de electrolizadores para producir 10 millones de toneladas/año. En el ámbito industrial, este hidrógeno será materia prima para procesos, entre los que destaca la fabricación de combustibles sintéticos.
El hidrógeno es un gas incoloro e inodoro, clasificado como extremadamente inflamable según la normativa en vigor. En efecto, para provocar la ignición del hidrógeno hace falta 15 veces menos energía que para el gas natural. Y el rango de concentraciones en el aire en los que el hidrógeno es inflamable –con llama invisible para el ojo humano– es 10 veces mayor que para la gasolina.
Estas propiedades hacen que las instalaciones industriales que generan, procesan y almacenan hidrógeno tengan asociado un determinado nivel de riesgo sobre elementos vulnerables (personas, medio ambiente e instalaciones o activos industriales), originado por eventos incontrolados. Y todo ello hace necesario disponer de las suficientes barreras de seguridad para evitarlos o minimizar sus consecuencias.
Es imprescindible conseguir altos niveles de seguridad en las instalaciones de hidrógeno verde: tanto en el diseño e ingeniería, como en su operación y mantenimiento, de manera que aseguremos la continuidad de la operación y del negocio.
Dadas las características del hidrógeno, el concepto de seguridad aplicable debe ir mucho más allá del mero cumplimiento de las obligaciones legales, los reglamentos industriales, la normativa técnica o los estándares de diseño. Se requiere, además, el empleo experimentado de herramientas avanzadas para la identificación, evaluación y gestión de los riesgos, como soporte para la administración y la toma de decisiones.
Este criterio es aplicado ya en la actualidad por los operadores de instalaciones que producen hidrógeno por otras vías –especialmente el denominado ‘hidrógeno gris, por reformado con vapor de metano– en refino, industria química y petroquímica. La aparición de la producción de hidrógeno por parte de nuevos actores de sectores distintos requiere, sin lugar a dudas, replicar los elevados estándares de seguridad puestos en práctica por estas actividades.
En la etapa de diseño e ingeniería, las plantas deben concebirse con seguridad intrínseca, para reducir al mínimo el riesgo tanto en su interior como en el exterior. Es clave en esta fase la realización de análisis de riesgos exhaustivos y la aplicación de técnicas adecuadas (HAZID/HAZOP, Análisis SIL y LOPA, FMECA, QRA, ALARP, BOW-TIE, etc.) para identificar todas las posibles situaciones de peligro.
El diseño debe incorporar, entre otras barreras de seguridad, la ubicación óptima de detectores de fuego e hidrógeno –para identificar los potenciales eventos peligrosos en fases tempranas–, activar los mecanismos de respuesta necesarios y mitigar las posibles consecuencias. Existen herramientas (Fire&Gas p.e.) que permiten una ubicación optimizada de los distintos tipos de sensores y es muy importante el diseño del tratamiento de las señales de medida y su transmisión, para que la activación de protocolos sea rápida y eficaz.
La operación requiere la implementación de sistemas de gestión de seguridad de procesos que garanticen el funcionamiento adecuado de los activos. Dichos sistemas se basan en dos pilares fundamentales: el compromiso de la organización con la seguridad y el conocimiento y gestión de los riesgos.
La necesaria planificación ante emergencias deberá establecer una respuesta organizada de todos los medios humanos y materiales para limitar las consecuencias en caso de accidente. Esta planificación, basada en la mejora continua, necesita de la formación teórica y práctica del personal clave y la realización de ejercicios y simulacros.
La integridad de activos (Asset Integrity) requiere la adopción de estrategias optimizadas de mantenimiento y fiabilidad de los equipos, las infraestructuras y las barreras de seguridad, con herramientas como las que establece la norma ISO 55000 para la optimización de las instalaciones. Dentro de ellas cabe destacar los Estudios RAM (Reliability, Availability and Maintainability), para la cuantificación de la probabilidad de potenciales fallos de los equipos, de manera que se estime la disponibilidad de la planta de generación de hidrógeno y se focalicen las acciones de mantenimiento con una óptima relación coste/beneficio.
En definitiva, la aplicación de herramientas para la identificación, evaluación y gestión de los riesgos en instalaciones de hidrógeno verde permite concebir instalaciones intrínsecamente seguras, identificar y evaluar los riesgos (el riesgo cero no existe), garantizar su adecuada gestión, minimizar la materialización de accidentes y establecer los mecanismos de respuesta para una mayor disponibilidad de los activos, contribuyendo así a la continuidad del negocio.
Resulta extraordinariamente importante que los promotores y operadores de proyectos de hidrógeno verde den un lugar preferente a su seguridad y riesgos en todo el ciclo de vida de los proyectos con el soporte de especialistas en los diferentes ámbitos descritos.
Que los objetivos de la Comisión y de los promotores de proyectos se cumplan depende, entre otros factores, de la creación de una industria del hidrógeno verde segura y fiable y en la que la aparición de ’showstoppers‘ se vea minimizada por una gestión solvente y experimentada, percibida así por las partes interesadas.