SAFETY ENGINEERING: SAFE DESIGN FROM INITIAL CONCEPTS TO OPERATION
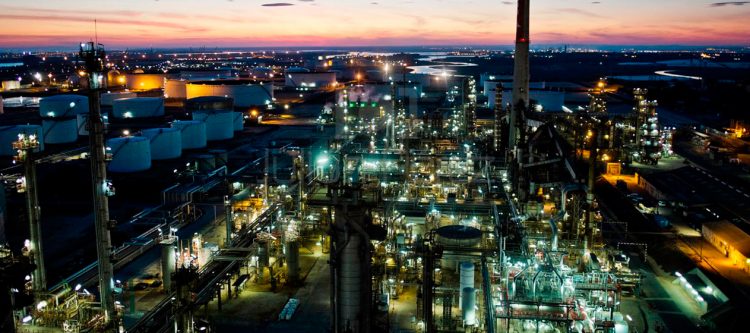
Oil&Gas plants are designed, built and operated safely with measures in place to ensure the protection of workers, the population and the environment. These measures are guaranteed by international standards in order to ensure the highest level of safety at these facilities. Today, specialised tools and methodologies can used to carry out hazard analysis at all project phases.
Countless tools are available, depending on which phase of engineering the project is at and the hazard management policy defined. These tools may be HAZID/HAZOP studies, failure mode effects analysis (FMEA), SIL analysis, quantitative risk analysis (QRA), RAMS analysis or risk-based inspections (RBI).
While national regulations do not require the application of these tools, an ever-growing number of companies in the sector are undertaking these studies in order to meet the standards governing the international Oil&Gas sector. This article offers an introduction to the most common tools that have been used and fully tested over the years.
HAZOP (HAZards and OPerability) analysis
Due to its systematic approach and multidisciplinary nature, HAZOP analysis has for decades been the most widely used tool for identifying and mitigating hazards in industry The objective of the technique is to identify all deviations from design conditions for the lines and elements belonging to a specific process unit that may lead to accidents or serious operability issues, with special focus on deviations that could cause accidents with serious consequences.
This identification of undesired consequences enables companies to define recommendations to improve a facility’s operability and safety, resulting in optimal efficiency and productivity. In this sense, the proposed modifications could affect monitoring and emergency systems, the conditions of line, equipment and instrument design and written procedures. Recommendations for specific detail studies could be derived from these proposals.
SIL (Safety Integrity Level) analysis, SIL verification and SRS (Safety Requirement Specifications)
The handling and movement of hazardous substances at facilities requires safety measures with demanding criteria for the infringement of pre-set conditions, in order that the process be run in conditions of safety for people, the environment and infrastructure. This translates to a need to implement special systems that are independent of any other system, in order that they may act in the event of other prevention systems failing and make the process safe.
These systems are called safety instrumented systems (SIS); the nature of these systems means they must have sufficient conditions of safety and reliability to ensure they function properly when they are required. This is the reason for the SIL analysis, which calculates the SIL (safety integrity level) index in order to assess the safety level required of those systems and verifies that they meet the required level.
HAZOP analyses and the implementation of SIS in process facilities after SIL analysis benefits companies in the following ways:
- Increased safety of facilities.
- Reduced insurance premiums.
- No lost guarantees; process safety conditions are maintened.
- Adaptation to functional security regulations, which constitute an engineering good practices guide.
- Compliance with risk acceptance criteria.
Reduced financial losses.
No Comment