Technology Solutions For The Environmental And Performance Optimisation Of Rotary Kilns
Introduction
One of the main challenges to be faced by the cement sector is the compliance with environmental legislation while maximising the economic profitability of its production process from the following viewpoints:
- Minimisation of capital and/or operating costs linked to new gas cleaning technologies.
- Minimisation of penalties, or even, improvement of overall energy efficiency.
- Adaptation to variable operating scenarios specially linked to the use of dissimilar fuels, including waste co-incineration and biomass co-firing.
In this context, INERCO is able to give response to these needs on the grounds of its extensive experience and know how in the optimisation of combustion process and in the handling and characterisation of pulverised solids. In addition, INERCO has also designed state-of-the-art monitoring technologies and has the capabilities to undertake the retrofit of combustion and milling systems and to supply a wide range of pollutant abatement technologies.
In this context, INERCO has carried out over 250 projects focused on the characterisation and optimisation of combustion process in more than 130 combustion units from Europe, North and South America, Far Asia and Northern Africa, which belong to cement, power, refining, petrochemical and metallurgic sector, among others.
This article summarises the main capabilities that can be provided by INERCO for the cement sector and includes a case study to demonstrate their potentiality.
INERCO’s solutions for the cement sector
Combustion optimisation
Efficiency and emissions in combustion units largely depend on the adequate reaction of fuel and air, including not only the fuel/air supply ratio but also their correct distribution within the combustion unit. Therefore, combustion effectiveness is directly linked to the actual balancing of the combustion process.
Taing this into account, INERCO has developed and demonstrated an innovative technological approach, the so-called ABACO technology, which relies on the closed-loop control of combustion based on the monitoring of local in-furnace conditions and the adequate regulation of combustion performance in combustion units, and more specifically, in rotary kilns (Figure 1).
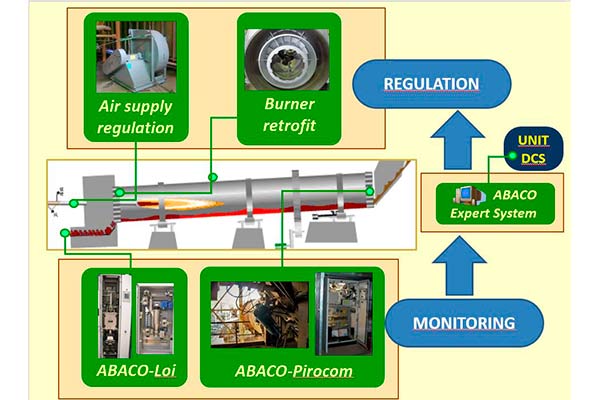
As represented in Figure 1, to reach optimised operating scenarios, the following elements are employed in an integrated approach:
- Advanced monitoring technologies, for the direct characterisation of flue gas concentration (O2, CO, CO2, NO) at kiln exit. To that aim, INERCO has developed ABACO-Pirocom monitoring technology, designed to withstand the extremely harsh conditions found in this location due to the extreme thermal conditions and the high dust concentration of corrosive and slag forming nature, which typically result in continuous probe material damage and gas in-take blockages.
ABACO-Pirocom combines simplicity and mature technology from best cutting-edge monitoring and control equipment in order to assure maximum accuracy and availability, reducing to its lowest the mandatory maintenance tasks while enhancing the manoeuvrability of the system.
ABACO-Pirocom is the distinctive technological solution which make possible the application of this approach and it is schematically represented in Figure 2.
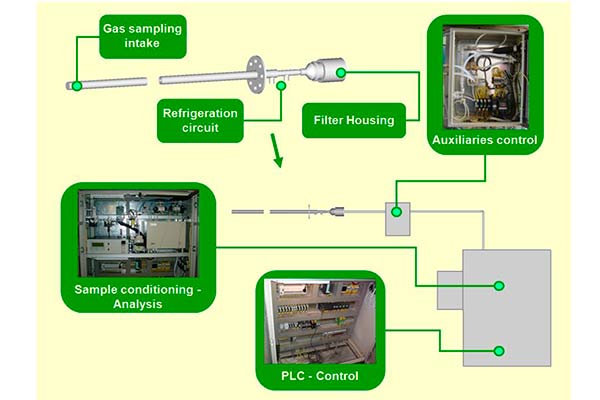
- Novel regulation systems for combustion optimization. Improvement of kiln tuning capabilities through the automation of existing manual regulations from control room or the revamping of existing equipment, such as burner nozzles or air inlet registers to increase their tuning potential based on advanced CFD modelling.
- Expert software for optimized combustion control. Closed-loop management and optimization of combustion process is performed through the establishment of optimized operating strategies in which available monitoring and regulation capabilities (existing and new tools) are integrated with the advanced ABACO combustion control system, which can be configured for each specific application, allowing combustion optimisation strategies to be applied with maximum reliability and profitability.
ABACO Expert System is individually configured by INERCO’s combustion experts for each combustion unit based on the basis of specific targeted testing devised in accordance with the final objective pursued by the facility, namely:
- Direct reduction of pollutant emissions.
- Fuel saving through the increase of combustion efficiency and the overall enhancement of global efficiency (heat exchange improvement, reduced consumption of auxiliaries, etc.).
- Achievement of uniform and stable operating conditions contributing to process reliability, optimum clinker production and quality, an improved performance of pollutant abatement technologies or the reduction of maintenance needs.
- Reduction of operating costs linked to lower reagent consumption in SNCR technology.
- Reliable adaptability to variable operating conditions and different fuel features.
Flue gas abatement technologies
INERCO has wide experience not only in the implementation and turnkey supply of NOx abatement technologies but also in the optimisation of existing gas cleaning systems
In order to minimise the investments associated with the implementation of NOx abatement technologies, the application of pre-catalytic measures, as SNCR technology, turns out to be the most attractive solution for cement sector (Figure 3).
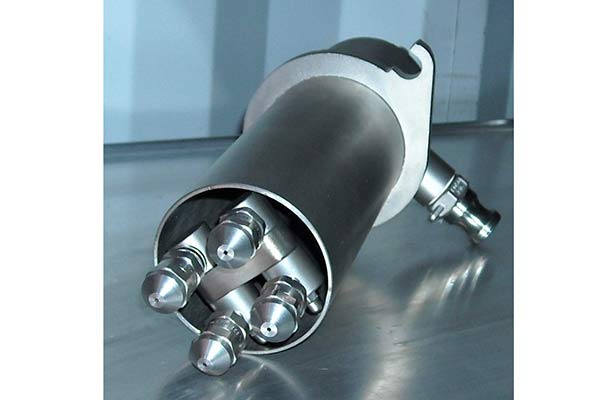
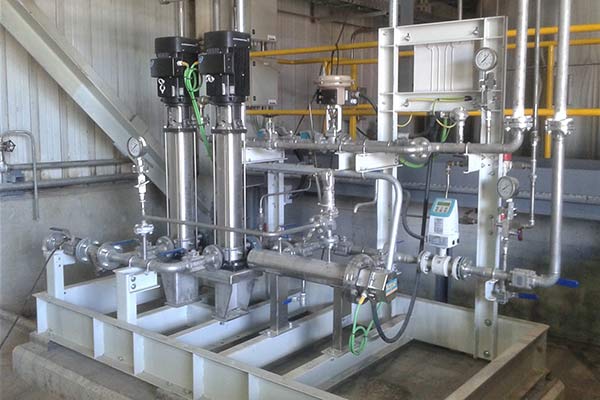
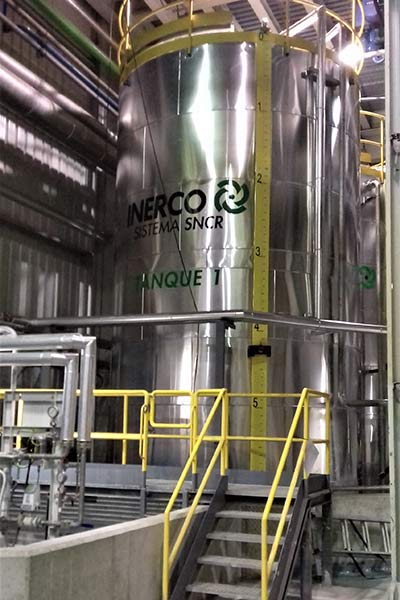
The profound knowledge about SNCR and the actual synergy with ABACO approach makes it possible to achieve maximum NOx reductions while limiting the consumption of ammonia-based reagents. The possibility to make a better use of reagents limits the potential appearance of quite severe operational problems, especially those derived from an excessive ammonia slip, including the odour associated with excessively high ammonia emissions, the stack plume visibility when burning fuels containing chlorine or sulphur compounds, or the build-up of ammonium bisulphite scales in the latter case.
Although INERCO advocates the application of non-catalytic technologies for cement sector, in the event that higher NOx reductions were required, INERCO also has the capability to provide catalytic solutions for NOx abatement.
In this specific context, the implementation of non-conventional tailor-made catalytic solutions, such as slip catalyst or SCR in-duct, turns up to be the most cost-effective solution as it really entails truly qualitative gap respecting conventional catalytic technologies as regard to investment and operating costs.
On the other hand, INERCO also has the potential to supply technologies for the individual or simultaneous abatement of other pollutants which currently are subject to the environmental constraints (or might be in the future), such as particulate matter, sulphur oxides (SOx), mercury or Volatile Organic Compounds (VOCs).
Process control
Many other complementary technology solutions and services are also offered by INERCO with the objective of improving process control in the cement sector, highlighting the following:
- Optimization of ball mills, including the development of characterisation and tuning tests (air/solid ratio, particle size distribution), definition of strategies for mill performance (classifier position, strategy of ball recharge, selection of liners, ball size distribution, etc.), and ultimately, the retrofit of mill and/or classifiers.
- Supply of automated samplers for the handling of pulverised solids.
- ABACO-LOI technology for the characterisation of cement quality based on the automated determination of Loss On Ignition.
- Optimisation and upgrade of cyclone heat exchangers.
- Improvement of control tools and routines, including the modernization or replacement of BMS or DCS.
- Continuous Emission Monitoring Systems (CEMS).
- CFD modelling for process diagnosis and optimisation.
Case Study: rotary kiln at a Spanish cement factory with available SNCR technology
INERCO has demonstrated the potential of ABACO approach by a comprehensive diagnosis of combustion performance in the rotary kiln of a Spanish cement factory and the assessment of SNCR system installed in the last stage of the preheater tower.
An initial testing trial was performed making use of the portable manual version of ABACO-Pirocom monitoring technology (Figure 4). These trials showed an inadequate combustion performance in the rotary kiln as excessively high and extremely variable O2 values were characterised. This fact jeopardised process stability and negatively affected the performance of SNCR system, which gave rise to the ineffective use of the reagent with typical utilisation efficiency values around 50%
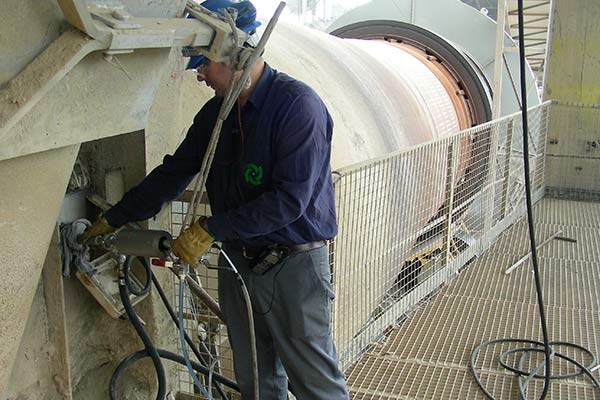
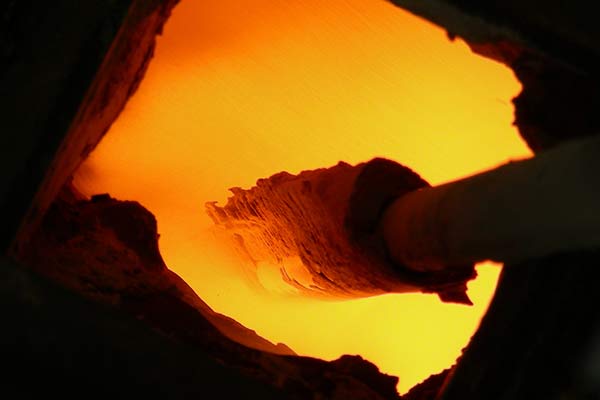
The development of a subsequent testing optimisation programme focused to the monitoring of combustion performance at the kiln exit, the reduction of O2 excess up to the minimum values compatible with process safety and stability and the balancing of reagent supply to the facility enabled the of the operational problems previously identified.
A representative graphic of the results achieved in this programme are shown in Figure 5.
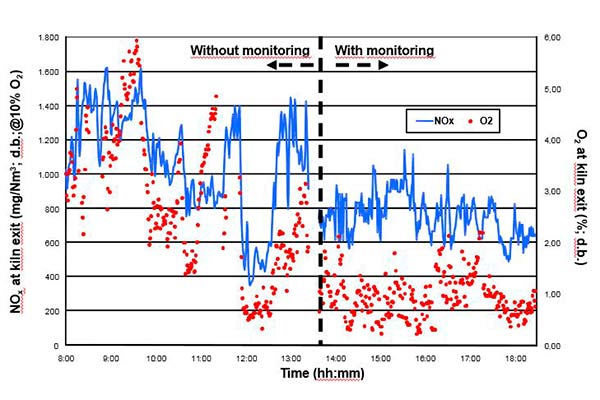
The analysis of Figure 5 shows how the use of ABACO-Pirocom monitoring technology clearly improved combustion performance, as O2 excess values were minimised and constrained within a highly controlled operating range, leading to reduced NOx generation, increased process efficiency and higher combustion stability. This increased stability, along with the balancing of reagent supply also made possible the enhancement of SNCR performance.
As a result, the achievement of similar overall NOx reductions was fulfilled in a much more efficient way due to a double effect. Firstly, a direct reduction in NOx generation ranging from 10% to 15% just by improved control over combustion performance. Secondly, SNCR effectiveness was increased around 20% up to utilisation efficiency values of 75%.
Finally, the subsequent action was the installation of ABACO-Pirocom technology for the automated monitoring of combustion performance. This has resulted in the reliable and steady control over combustion process.
Figure 6 shows images of ABACO-Pirocom monitoring technology installed at the target cement factory.
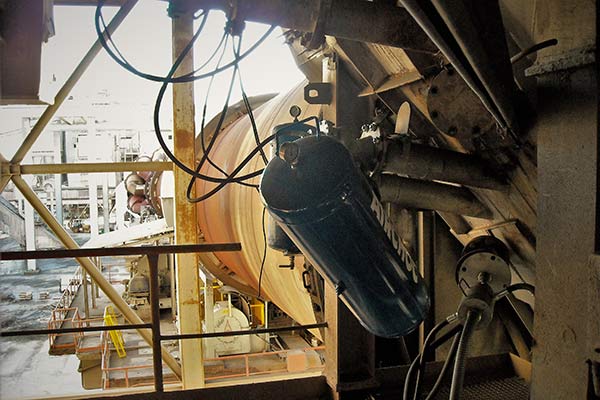

Conclusions
When facing the overall optimisation of production process in cement factories, INERCO has a wide portfolio of products and solutions that may contribute to achieve the environmental, efficiency and operational improvement of cement manufacture. Among them, it can be highlighted the implementation of advanced monitoring and control technologies for combustion optimisation, the turnkey supply of pollutant abatement technologies or a number of options to enhance different aspects of cement manufacturing process.
The approach described in this paper has focused on the state-of-the-art ABACO-Pirocom monitoring technology, designed to withstand the extremely severe operating conditions of rotary kilns, which provides plant operators with critical and reliable information for promoting increased combustion stability and reduced pollutant emissions. Further positive effects are also brought about on production features, the performance of other pollutant abatement technologies and unit availability.
The application of this approach in a Spanish cement factory has resulted in the achievement of improved sustainable combustion conditions (stable O2 excess values continuously kept below 2%), the direct reduction of NOx generation due to the safe reduction of O2 excess (NOx reductions ranging from 10% to 15%), the improvement of energy efficiency due to the reduced consumption of auxiliaries, (also leading to additional reductions in the emission of all pollutants) and the improved performance of existing SNCR system (with an increased reagent utilisation up to values around 75%).
Source: https://www.cemnet.com/