Safety in the green hydrogen industry
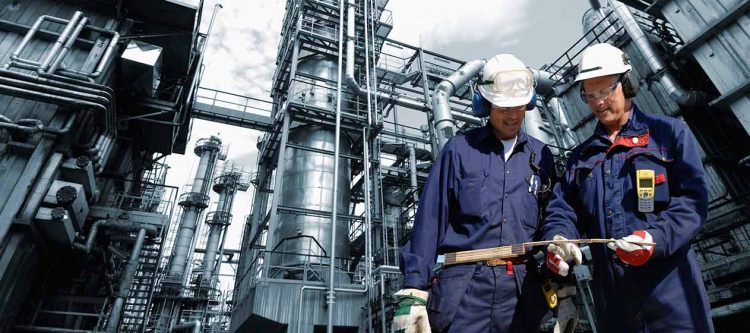
The EU’s Green Deal sets a target of reducing greenhouse gas (GHG) emissions by 50% by 2030, requiring a rapid process of decarbonization of the economy. To this end, among other lines of action, in July of this year the European Commission published the European Hydrogen Strategy (COM (2020) 301 final), in which the production of green hydrogen by electrolysis of water using renewable electricity is the key technology.
The Commission’s strategy aims to make hydrogen an intrinsic part of an integrated energy system with at least 40 GW of electrolysis to produce 10 million tons/year by 2030. In the industrial field, this hydrogen will be a raw material for processes, including the manufacture of synthetic fuels.
Hydrogen is a colorless and odorless gas, classified as extremely flammable according to the regulations in force. In fact, it takes 15 times less energy to ignite hydrogen than natural gas. And the range of concentrations in the air in which hydrogen is flammable – with a flame invisible to the human eye – is 10 times greater than for petrol.
These properties mean that industrial facilities that generate, process and store hydrogen have a certain level of risk associated with vulnerable elements (people, the environment and industrial facilities or assets), caused by uncontrolled events. And all this makes it necessary to have sufficient safety barriers to avoid them or minimize their consequences.
It is essential to achieve high levels of safety in green hydrogen facilities: both in design and engineering, and in operation and maintenance, so as to ensure continuity of operation and business.
Given the characteristics of hydrogen, the applicable safety concept must go far beyond mere compliance with legal obligations, industrial regulations, technical standards or design standards. It also requires the experienced use of advanced tools for the identification, evaluation and management of risks, as a support for administration and decision making.
This criterion is already being applied by operators of plants producing hydrogen by other means – especially so-called ‘grey hydrogen, by reforming with methane steam’ – in refining, the chemical and petrochemical industry. The emergence of hydrogen production by new players from different sectors undoubtedly requires a replication of the high safety standards put in place by these activities.
At the design and engineering stage, plants must be designed to be intrinsically safe, to minimize risk both inside and outside. It is key in this phase to carry out exhaustive risk analyses and to apply appropriate techniques (HAZID/HAZOP, SIL and LOPA analyses, FMECA, QRA, ALARP, BOW-TIE, etc.) to identify all possible danger situations.
The design must incorporate, among other safety barriers, the optimal location of fire and hydrogen detectors – to identify potential hazardous events at an early stage – to activate the necessary response mechanisms and to mitigate possible consequences. There are tools (e.g. Fire&Gas) that allow an optimized location of the different types of sensors and it is very important to design the treatment of the measurement signals and their transmission, so that the activation of protocols is quick and efficient.
The operation requires the implementation of process safety management systems to ensure the proper functioning of the assets. These systems are based on two fundamental pillars: the organization’s commitment to safety and the knowledge and management of risks.
The necessary emergency planning should establish an organized response of all human and material means to limit the consequences in the event of an accident. This planning, based on continuous improvement, requires theoretical and practical training of key personnel and the carrying out of exercises and drills.
Asset Integrity requires the adoption of optimized strategies for the maintenance and reliability of equipment, infrastructure and safety barriers, with tools such as those established by the ISO 55000 standard for the optimization of facilities. Among them, it is worth highlighting the RAM (Reliability, Availability and Maintainability) Studies, for the quantification of the probability of potential equipment failures, so that the availability of the hydrogen generation plant is estimated and maintenance actions are focused with an optimum cost/benefit ratio.
In short, the application of tools for the identification, evaluation and management of risks in green hydrogen installations makes it possible to design intrinsically safe installations, identify and evaluate risks (there is no such thing as zero risk), guarantee their proper management, minimize the occurrence of accidents and establish response mechanisms for greater availability of assets, thus contributing to business continuity.
It is extremely important that the promoters and operators of green hydrogen projects give priority to their safety and risks throughout the life cycle of the projects with the support of specialists in the different areas described.
Whether the objectives of the Commission and project developers are met depends, among other factors, on the creation of a safe and reliable green hydrogen industry in which the emergence of ‘showstoppers’ is minimized by sound and experienced management, as perceived by stakeholders.